Our professional R&D team brings over 10 years of experience in developing automated systems, continuously driving technological innovation and product upgrades. Through close collaboration with Great Bay University, we have advanced the key technologies for fully automated flexible manufacturing systems for metal wire products. Notable achievements include the development of patented technologies such as the horizontal dual-station-controlled shared wire automation packaging system and feeding system of the vertical packaging machine .
By scaling these innovations, we are driving the industry’s shift from traditional management methods to advanced, data-driven systems, greatly improving the efficiency and quality of metal wire and coil packaging.
The metal wire industry has long been dependent on manual labor, particularly in the packaging stage, leading to several inefficiencies such as low production output, substandard product quality, high material waste, and unsafe production processes. The industry has also faced challenges with process coordination and a lack of automation.
To address these issues, Siao has partnered with Great Bay University to establish a dedicated R&D team focused on overcoming these challenges through automation and intelligent systems. By combining expertise in mechanical design, automation control, Internet of Things (IoT), data processing, and computer programming, the team is working on developing a fully automated, intelligent, and digitalized wire wrapping and packaging system. This innovation aims to improve the overall quality of metal wire packaging, close existing technology gaps, and support the high-quality development of China’s manufacturing industry. Ultimately, these advancements contribute to technological progress and economic growth through automation.
The development of the automated packaging system for metal wires was led by Dr. Duan, a renowned expert in intelligent technology design and manufacturing, with significant investment from Great Bay University. The project was launched in 2012 and has since successfully developed and refined the wire coil packaging equipment, pushing the boundaries of automation and flexible manufacturing for the metal wire industry.
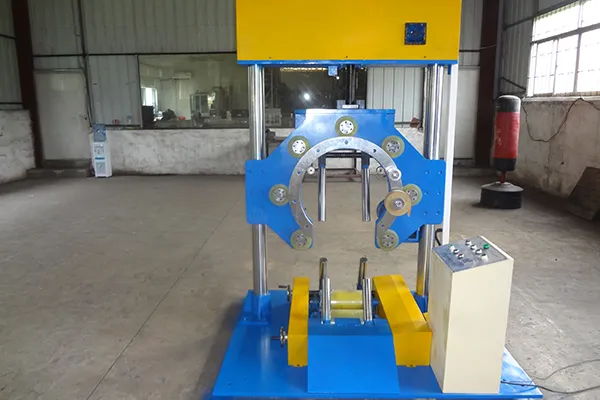
Developed the first manual packaging machine, which required manual assistance, resulting in low efficiency.
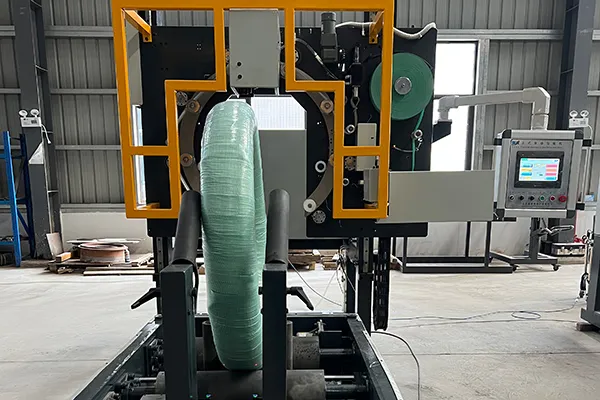
Launched the semi-automatic packaging system, where manual feeding to the machine was followed by automatic packaging. This improvement significantly reduced labor intensity in the packaging process.
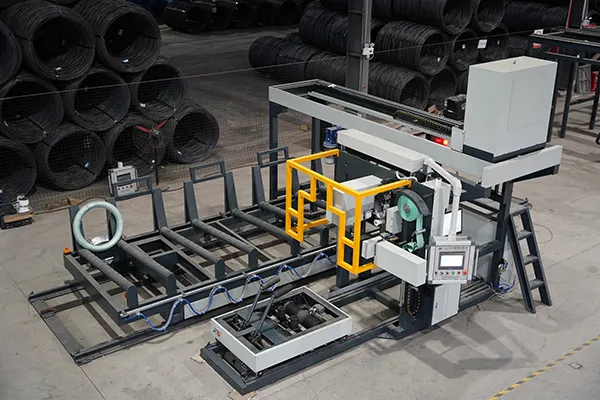
Introduced the fully automatic vertical packaging line, where manual input was limited to feeding material, with packaging, weighing, labeling, and palletizing all automated.
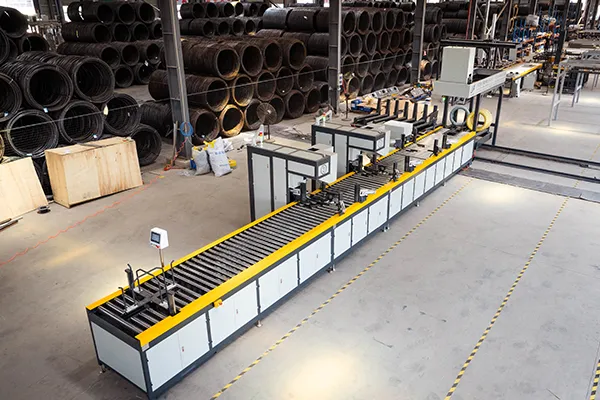
Upgraded to an automatic lifting material cart with automated conveying, weighing, labeling, and palletizing, resulting in a significant increase in packaging efficiency.
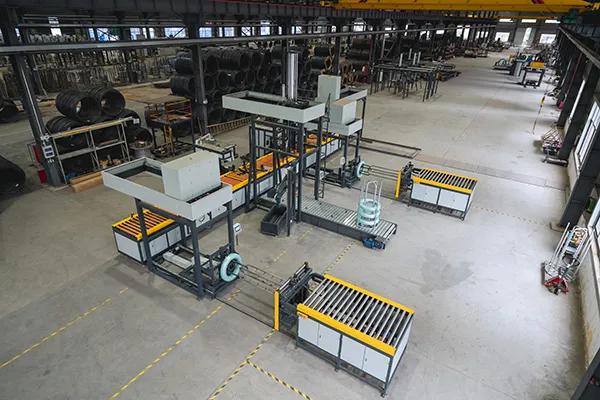
Developed a system capable of handling different metal wire products with tailored feeding methods, automating packaging, weighing, labeling, and specification-based classification for storage.

Created the integrated wire drawing and packaging production line, combining wire drawing and packaging into a single automated process.
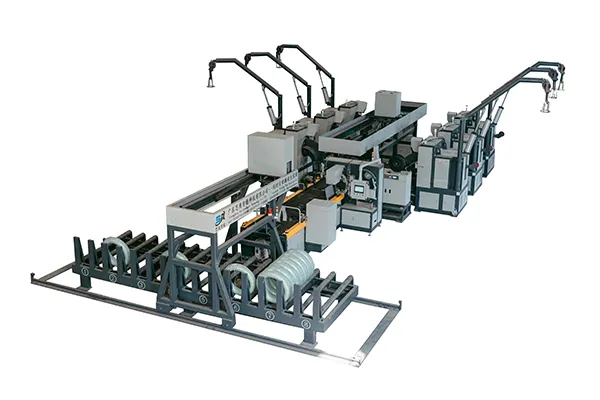
Upgraded the fully automated packaging production line, increasing from two to six dead block drawing coilers, all utilizing a shared packaging line.
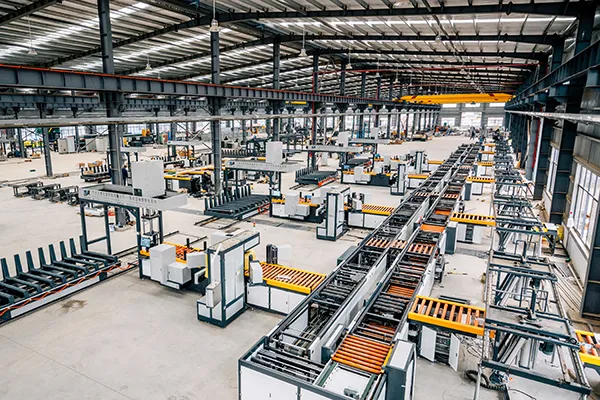
Developed a combined packaging line that integrates dead block and inverted bull block wire drawing machines, customized to meet varying customer needs and optimizing space efficiency.
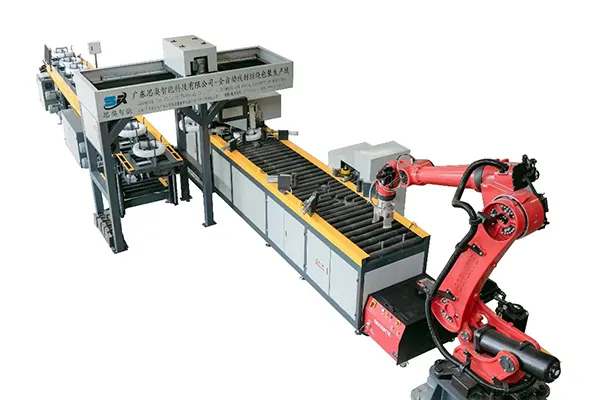
Integrated industrial robotic arms into the packaging line, enabling unmanned packaging and palletizing, achieving a new level of automation in packaging.
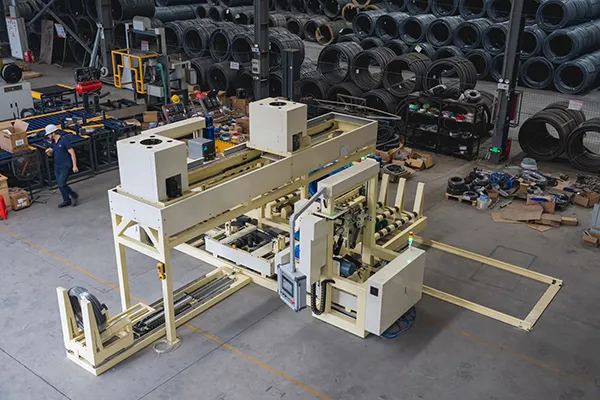
Launched an upgraded vertical packaging line, further improving automation and efficiency in the packaging process.
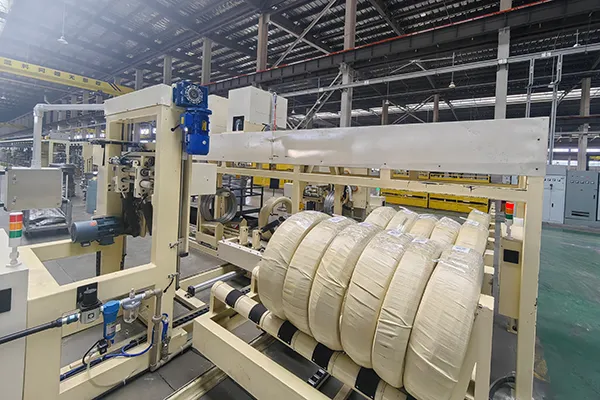
Introduced AGV (automated guided vehicle) systems for material handling, transforming the packaging line into a fully intelligent production system. This new packaging mode has revolutionized the market by offering fully automated transportation and packaging processes.
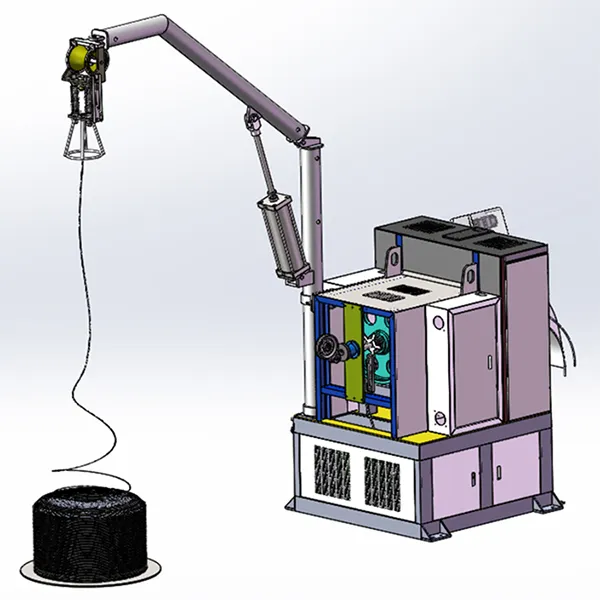
Function
Our wire drawing system is designed to meet customer specifications, allowing for the compression of wire to the required size and weight for different products.
Technical advantages
- Equipped with safety mechanisms that halt operations when the wire is tangled or knotted at the entry point, ensuring safe operation.
- Automatically calculates the weight as it feeds, ensuring precise material handling and reducing the risk of human error.
- Automatically cuts the wire once the desired weight is reached, integrating wire collection and weight calculation. This eliminates the need for manual wire cutting, simplifying operations and boosting production efficiency.
- With the introduction of automation, one operator can now manage six or more machines simultaneously, compared to one operator handling just two manual units, resulting in a significant reduction in labor costs.
Function
The system automatically transfers the wire coild after drawing to the next stage for bundling.
Technical advantages
- When multiple products from the drawing machine arrive simultaneously, the system automatically queues them in sequence, preparing for the next step in the process.
- The system ensures a smooth, sequential transfer of products, automatically preparing them for bundling.
- By replacing manual crane and hoist operations with automated gripping and transfer, it significantly simplifies the transfer process, improving operational efficiency and reducing the need for manual intervention.
- The automatic bundling feature replaces the manual bundling process, simplifying operations, increasing production efficiency, and substantially reducing labor costs.
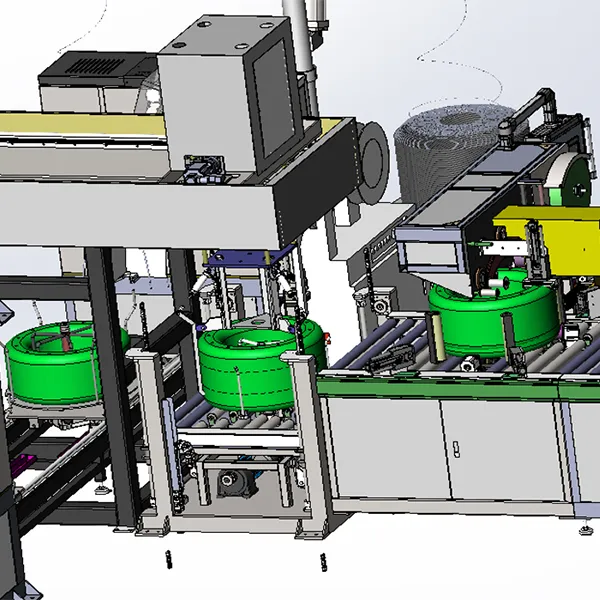
Function
This system is designed to wrap and package bundled wire coils according to specific process requirements.
Technical advantages
- When feeding continuously, the system automatically queues products in sequence for wrapping, ensuring a smooth, efficient workflow.
- The system offers four distinct packaging modes based on customer requirements:
Standard mode: Wraps with braided tape and seals the tail with PE film
Full wrap mode: First wraps with braided tape, then fully covers with PE film
Dual-wrap mode: Starts with PE film, then wraps with braided tape, and seals the tape tail with PE film
PE film only mode: Wraps with PE film only - By replacing manual wrapping with automated coil wrapping, this system significantly simplifies the packaging process, improving production efficiency and reducing labor costs.
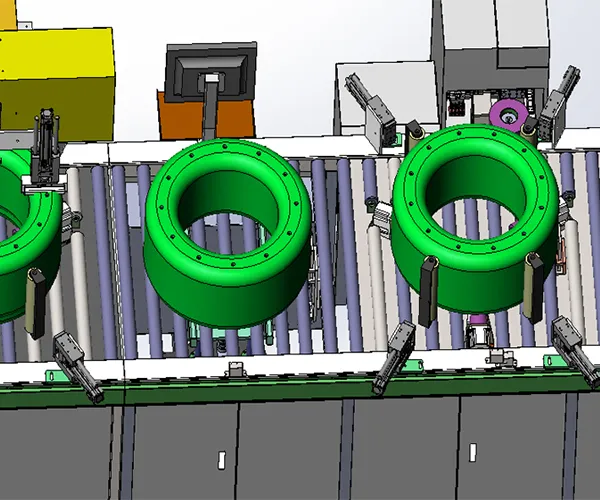
Function
This system is designed to recheck the weight of wrapped products and apply labels according to specified requirements.
Technical advantages
- When feeding continuously, products are automatically queued for weighing in sequence.
- The system verifies if the loaded weight matches the set value. If the weight deviates beyond the allowable margin, the system triggers an alarm to alert the operator for necessary adjustments.
- Replacing manual weighing and labeling with automated processes, the system significantly simplifies operations, improving production efficiency and reducing labor costs.
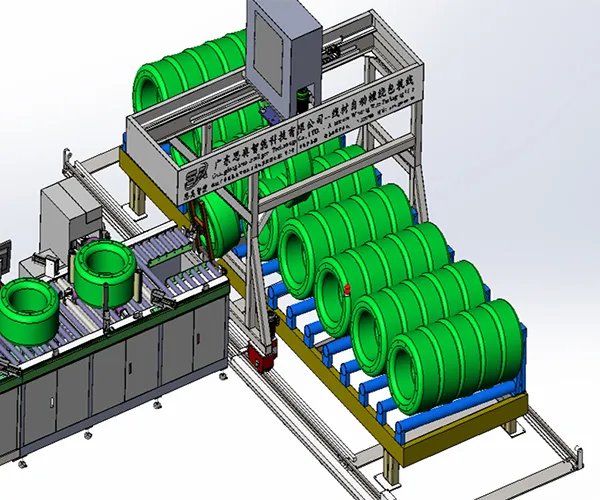
Function
This system is designed to temporarily store qualified metal wire coils in the appropriate positions according to process requirements.
Technical advantages
- Bundled metal wire coils are automatically queued in sequence for intermediate transfer during continuous feeding.
- The wire coils are palletized and stored based on configurable criteria such as production time, batch numbers, weight, specifications, or customer information.
- By replacing manual palletizing with automated transfer and storage, this system simplifies the workflow, boosts production efficiency, and significantly reduces labor costs.
In metal wire coil wrapping equipment, the control system collaborates seamlessly with sensors, controllers, and actuators, using advanced algorithms to perform the following functions:
- Packaging mode setup and control
The system allows for the simultaneous setup of four different packaging modes. Based on predefined conditions, the system automatically initiates the packaging process when the product meets the set criteria. This feature reduces the need for manual verification, minimizing the risk of errors and optimizing both product appearance and packaging quality. - Data collection and analysis
The system collects data during operation and compiles decision-making results into a centralized data management system. Users can query detailed data such as order numbers, machine IDs, production time, product specifications, and storage locations. - Product management
The product management system allows for efficient, date-based searches, ensuring effective and organized management of all processed products. - Equipment warnings
The real-time monitoring feature, powered by sensors, enables the system to detect and report abnormal conditions promptly, ensuring safe and smooth equipment operation at all times. - Production process optimization
The system utilizes precision algorithms to continuously optimize the production workflow, enhancing both efficiency and product quality.
- Equipment operation monitoring
The system provides real-time monitoring of equipment operation, ensuring that the machines run at their optimal performance. It helps identify and resolve potential issues before they affect production. - Event exception and alarm recording
All exceptional events and alarm information that occur during operation are recorded and displayed. This allows operators to take timely action to maintain safe and stable production processes. - Multi-device collaborative control
The system enables the connection and collaborative control of multiple feeding and drawing modules. By generating and sending scatter commands, the system optimizes the manufacturing process, improving production efficiency, reducing labor costs, and minimizing operational errors.